Necessary Coating of Super Magnets
Neodymium is easily to react to oxygen and oxidises quickly if untreated. That's why all neodymium magnets are covered with a protective coating, which is so thin that it doesn't have any impact on the adhesive force of the magnet.
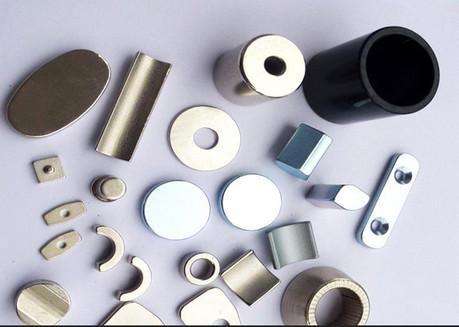
We use the following coatings on our neodymium magnets:
Nickel (Ni-Cu-Ni)
It is the most common plating. Ni-Cu-Ni is a durable 3 layer (nickel, copper, nickel coating). Great for indoor use. They may be used outdoors if protected from rain and humidity. Good abrasion resistance.
Gold-coating (Ni-Cu-Ni-Au)
Gold-coating has highly corrosion resistant and conductive. It usually coated with a base layer of Nickel, and copper, to bring out the natural shine of the gold. It works very well in water applications. The gold layer is very but still adds some cost to the magnet.
Chrome (Ni-Cu-Ni-Cr)
The chrome has better resistance against rubbing and pressure, that's why we use this coating for our sphere magnets, its colour is dull, grey-metallic.
Copper (Ni-Cu)
Its color is shiny brown-red-gold. The color may change over time due to oxidation (darkening, spots).The copper-colored surface rubs off with frequent use (similar to gold-coated magnets) and is therefore suitable for decorative purposes only.
Epoxy resin (Ni-Cu-Ni-Epoxy)
Black Epoxy plating is consists of 3 layers Nickel, Copper, and Epoxy exposed as the top layer. Great for outdoor applications. However, black epoxy is not as abrasion resistant as other platings. In harsh conditions the epoxy layer may be scrached off to expose the copper layer underneath.
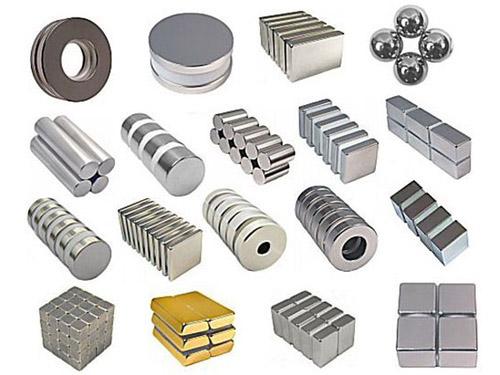
Even the smallest, not visible to the eye, damages of the coating will cause damage to the neodymium bar magnets in the long term when exposed to moisture.
Pre: How Does a Magnetic Compass Work in an Airplane
Next: High Strength Permanent Magnet King -NdFeB